Discover What is Porosity in Welding and Its Impact on Structural Integrity
The Scientific Research Behind Porosity: A Comprehensive Guide for Welders and Fabricators
Comprehending the elaborate devices behind porosity in welding is critical for welders and producers making every effort for impressive craftsmanship. From the structure of the base materials to the complexities of the welding procedure itself, a wide variety of variables conspire to either worsen or minimize the presence of porosity.
Recognizing Porosity in Welding
FIRST SENTENCE:
Examination of porosity in welding reveals important understandings into the integrity and high quality of the weld joint. Porosity, defined by the presence of cavities or spaces within the weld metal, is an usual problem in welding procedures. These voids, if not properly resolved, can jeopardize the structural honesty and mechanical residential or commercial properties of the weld, resulting in prospective failures in the completed product.
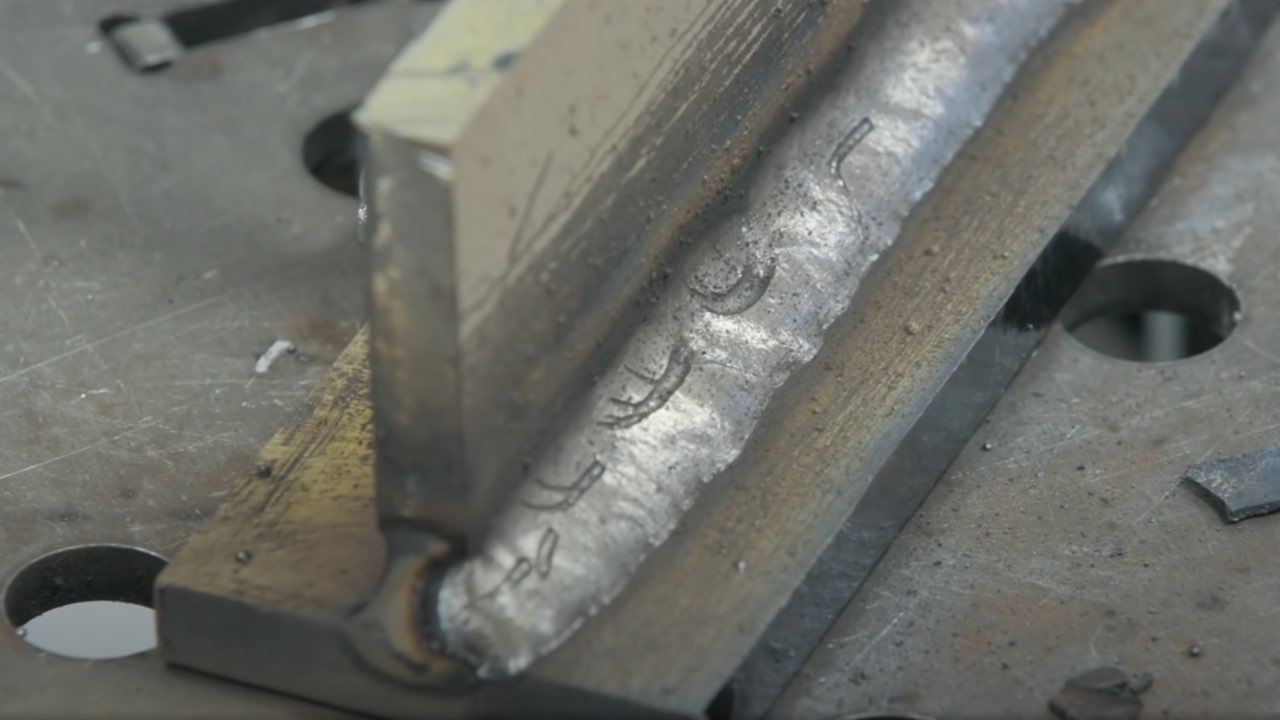
To detect and quantify porosity, non-destructive testing methods such as ultrasonic screening or X-ray evaluation are frequently employed. These strategies enable the identification of inner issues without jeopardizing the stability of the weld. By examining the size, shape, and circulation of porosity within a weld, welders can make informed decisions to enhance their welding processes and attain sounder weld joints.
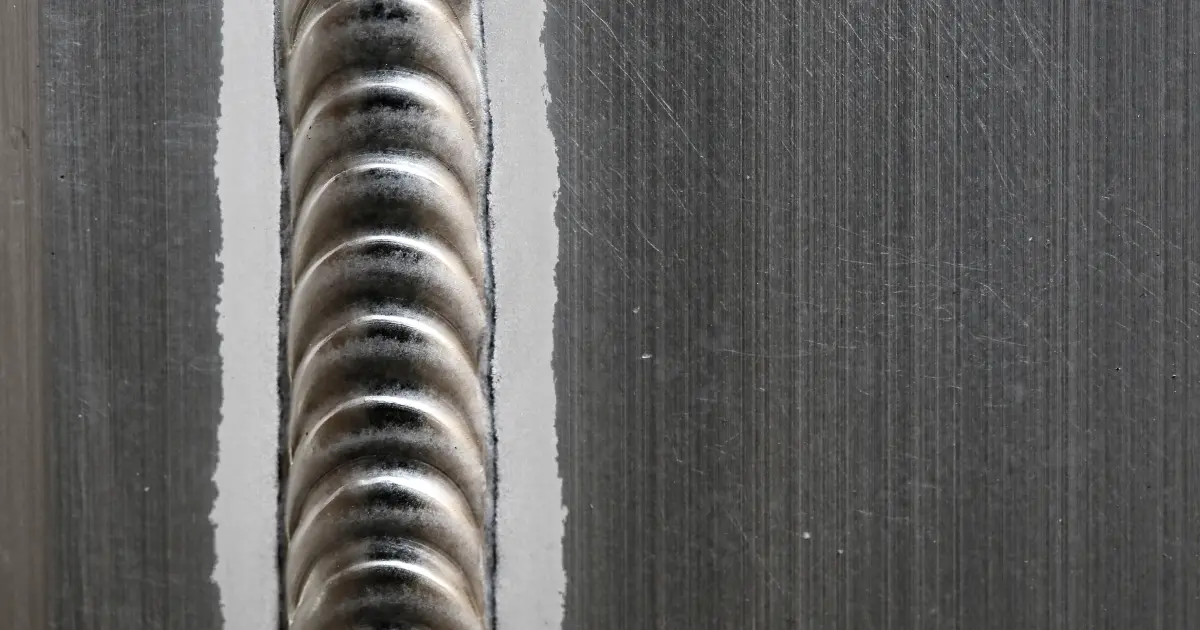
Variables Affecting Porosity Development
The incident of porosity in welding is influenced by a myriad of variables, varying from gas shielding performance to the complexities of welding parameter setups. One crucial element adding to porosity development is inadequate gas securing. When the protecting gas, typically argon or CO2, is not successfully covering the weld pool, climatic gases like oxygen and nitrogen can pollute the molten steel, leading to porosity. Furthermore, the tidiness of the base materials plays a significant role. Impurities such as rust, oil, or wetness can vaporize during welding, producing gas pockets within the weld. Welding specifications, consisting of voltage, current, travel rate, and electrode kind, also effect porosity development. Making use of incorrect setups can generate too much spatter or warm input, which in turn can cause porosity. Moreover, the welding method used, such as gas metal arc welding (GMAW) or protected metal arc welding (SMAW), can influence porosity development as a result of variations in heat circulation and gas protection. Understanding and managing these variables are vital address for minimizing porosity in welding procedures.
Impacts of Porosity on Weld High Quality
The visibility of porosity additionally compromises the weld's resistance to rust, as the entraped air or gases within the spaces can respond with the surrounding setting, leading to degradation over time. In addition, porosity can hinder the weld's capability to hold up against pressure or impact, additional threatening the general quality and reliability of the bonded structure. In critical applications such as aerospace, auto, or structural buildings, where security and resilience are vital, the destructive impacts of porosity on weld quality can have serious consequences, emphasizing the importance of minimizing porosity via correct welding methods and treatments.
Techniques to Reduce Porosity
To boost the top quality of bonded joints and make certain architectural stability, welders and makers use certain strategies focused on minimizing the formation of voids and tooth cavities within the material throughout the welding procedure. One efficient approach to reduce porosity is to guarantee appropriate material prep work. This includes detailed cleansing of the base steel to remove any pollutants such as oil, grease, or dampness that can add to porosity formation. Furthermore, making use of the proper welding specifications, such as the proper voltage, existing, and travel speed, is essential in preventing porosity. Maintaining a constant arc length and angle throughout welding likewise helps reduce see this page the probability of porosity.

In addition, picking the right protecting gas and maintaining correct gas flow prices are crucial in decreasing porosity. Using the suitable welding strategy, such as back-stepping or utilizing a weaving motion, can additionally help disperse warmth equally and minimize the opportunities of porosity development. Finally, go to the website guaranteeing appropriate ventilation in the welding environment to eliminate any potential resources of contamination is crucial for attaining porosity-free welds. By executing these methods, welders can effectively reduce porosity and create top quality bonded joints.

Advanced Solutions for Porosity Control
Implementing innovative innovations and innovative approaches plays an essential role in attaining remarkable control over porosity in welding procedures. One sophisticated solution is making use of innovative gas mixes. Shielding gases like helium or a mix of argon and hydrogen can aid minimize porosity by providing far better arc security and improved gas insurance coverage. Furthermore, utilizing advanced welding methods such as pulsed MIG welding or modified ambience welding can also help alleviate porosity issues.
An additional innovative service entails making use of advanced welding tools. Using equipment with built-in functions like waveform control and sophisticated power resources can boost weld top quality and lower porosity risks. The implementation of automated welding systems with specific control over specifications can substantially minimize porosity issues.
Furthermore, incorporating innovative surveillance and assessment innovations such as real-time X-ray imaging or automated ultrasonic testing can aid in detecting porosity early in the welding process, enabling prompt corrective activities. Generally, integrating these innovative remedies can significantly boost porosity control and boost the total top quality of bonded elements.
Conclusion
Finally, recognizing the scientific research behind porosity in welding is vital for welders and makers to create premium welds. By identifying the elements influencing porosity development and implementing techniques to decrease it, welders can boost the general weld high quality. Advanced solutions for porosity control can additionally boost the welding procedure and guarantee a solid and dependable weld. It is essential for welders to constantly inform themselves on porosity and execute finest techniques to accomplish optimum results.